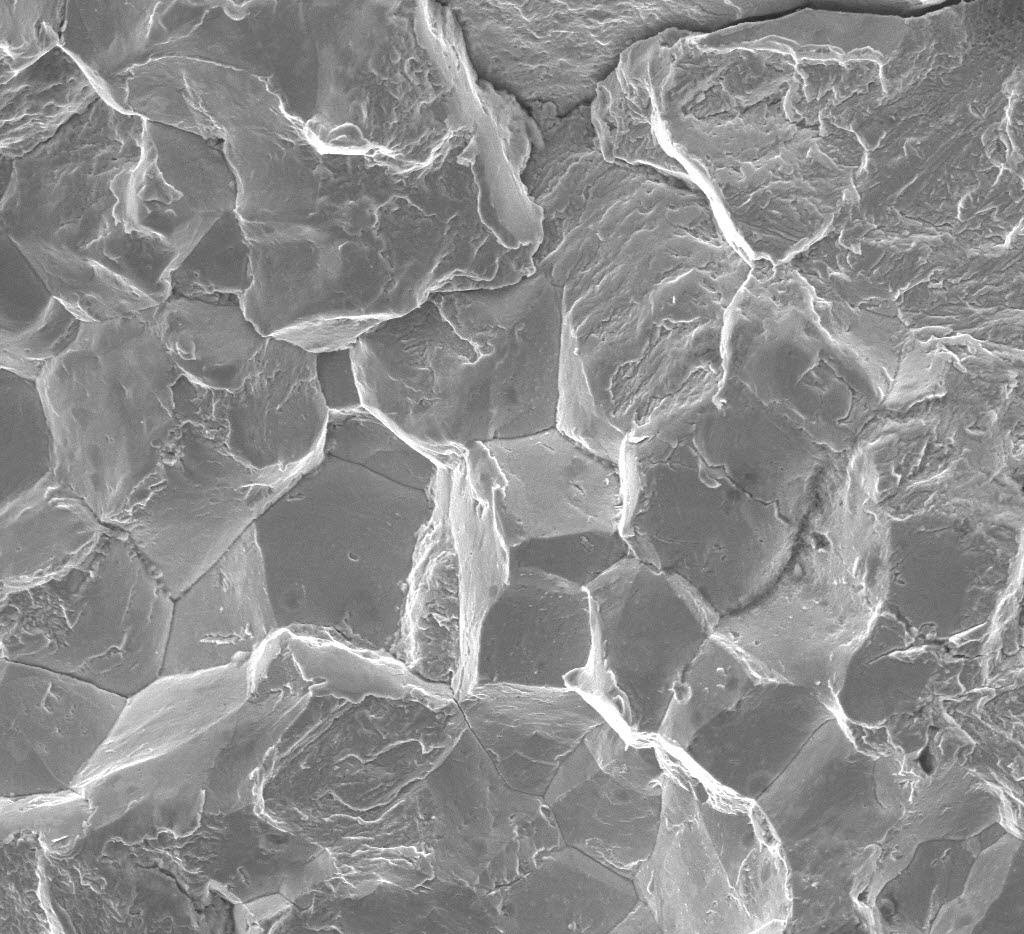
Overview
At Hurst Metallurgical, our staff members have extensive experience and knowledge in conducting metallurgical analyses in order to determine the root cause of failure, and to provide corrective recommendations for preventing failures and improving system performance.
Component Level Analysis
We have conducted trouble-shooting and metallurgical analyses to solve the problems of thousands of different products, including:
Parts made from steel, stainless steel, aluminum alloys, copper alloys, nickel alloys, titanium alloys, and zinc alloys
Aerospace components
Oil & gas system components
Pistons, rods, shafts, bearings, gears, springs
Pipes and pipelines
Forgings, castings, cold formed parts
Fasteners
Springs
Heat exchangers
Orthopedic implants
We also provide in depth analysis for the purpose of reverse engineering components. We can determine a part’s alloy composition, heat treatment, coating, and manufacturing method, to allow you to successfully reproduce the part.
System Level Analysis
In addition to component failure investigation, we have conducted large scale investigations on petroleum refinery explosions and large structures such as drilling rigs, crude oil pipelines, and construction cranes.
In-plant consultation and troubleshooting is available from our experienced metallurgical staff members to solve your manufacturing problems.
Assessing Your Needs
If you are interested in our analysis services, we are happy to schedule a phone call with you to discuss your needs and determine an initial scope of services that will be needed. Once we have performed an initial examination of the failed component(s), a comprehensive metallurgical test protocol and a fee estimate is provided to you up front for your approval. See our FAQ below for more information.
FAQ
-
Investigation timeframes vary based on complexity and available information. Most investigations take between 2-4 weeks to complete. We can provide an estimated timeframe for your project upon inquiry.
-
We can provide you with a free estimate after an initial consultation and review of the available background information such as circumstances leading to the failure, photographs, drawings, and standards.
-
We typically provide status updates at key milestones, such as initial assessment, after testing and evaluation, and final report completion.
-
A failure investigation begins with an initial conversation to understand the failure event and your objectives. We gather detailed information about the part or system’s history, including its material specifications, service conditions, and any prior issues. Our investigation typically includes a thorough visual inspection to identify surface anomalies, followed by non-destructive testing, metallurgical analysis, and, if needed, advanced techniques like SEM or EDS. Throughout the process, we keep you informed and deliver clear, actionable findings tailored to your needs.
-
We investigate a wide range of failures across various industries. These include mechanical failures such as fatigue, fracture, and overload; material failures like corrosion, hydrogen embrittlement, and wear; manufacturing-related issues such as heat treatment defects, quench cracks, or machining errors; and service-related problems, including stress corrosion cracking, thermal damage, and improper installation. Whether the failure involves metals, welds, coatings, or assemblies, we have the expertise to identify root causes and provide actionable solutions.
-
Yes, we take confidentiality very seriously. All information, data, and findings related to your investigation are handled with the utmost care and will not be shared with any third parties without your explicit consent. We can also provide a non-disclosure agreement (NDA) to ensure your sensitive information and intellectual property remain fully protected throughout the investigation process. Your trust and privacy are our top priorities.